The Value of Thorough Welding Assessment in Industrial Applications
In the world of industrial applications, the importance of thorough welding evaluation can not be overstated. It plays an essential function in guaranteeing the architectural honesty and durability of bonded parts. Advanced non-destructive screening techniques permit the very early detection of possible problems, such as fractures and incomplete blend, which, if left unattended, could lead to devastating failings. Moreover, adherence to stringent sector criteria not only ensures high quality however also develops client self-confidence. As we discover the multifaceted advantages of attentive welding assessments, one need to take into consideration the wider implications on safety, integrity, and cost-effectiveness in commercial procedures.
Enhancing Structural Honesty
When it comes to welding assessment in industrial applications, enhancing structural stability is vital. The main goal of welding evaluation is to make certain that the welds are capable of birthing the expected anxieties and lots they will certainly experience in service.
The importance of keeping structural stability in bonded frameworks can not be overemphasized. Improperly implemented welds can bring about tragic failures, causing expensive fixings, downtime, and also endangerment of human lives. For that reason, inspectors play an essential function in the lifecycle of commercial elements, giving guarantee that the welding procedure provides the wanted strength and resilience.
Furthermore, progressed modern technologies, such as phased selection ultrasonic screening and digital radiography, deal boosted capacities in finding possible weak points, permitting corrective steps before concerns rise. By focusing on the honesty of welds with precise examination, sectors can make sure functional efficiency and expand the durability of their infrastructure.
Identifying Welding Defects
Recognizing welding defects is a vital aspect of guaranteeing the safety and integrity of welded structures. Typical welding defects include porosity, splits, insufficient blend, and damaging.
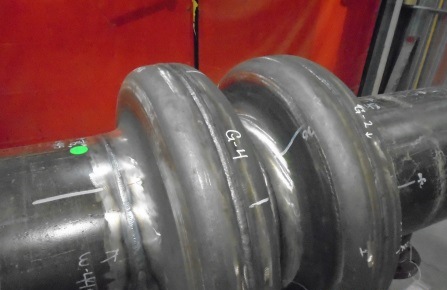
Experienced inspectors make use of both visual evaluation and advanced non-destructive screening (NDT) approaches, such as radiographic or ultrasonic screening, to identify these defects. The prompt recognition and rectification of welding issues are imperative to maintain the architectural honesty and longevity of industrial parts.
Making Sure Conformity Requirements
Maintaining the integrity of welded structures extends beyond determining flaws; it needs adherence to rigid conformity criteria. Conformity with well-known criteria, such as those provided by the American Welding Culture (AWS) and the International Company for Standardization (ISO), makes certain that welds fulfill minimum safety and quality requirements. These standards incorporate a large range of standards, consisting of product specs, welding procedures, and qualification of welders. Adherence to these standards is crucial to prevent structural failings, which can cause disastrous repercussions in industrial applications.
Regular audits and inspections are necessary in verifying conformity. Inspectors need to possess a detailed understanding of the relevant criteria and be adept at utilizing various non-destructive testing (NDT) approaches to evaluate weld high quality. By ensuring that welding methods straighten with compliance requirements, firms reduce the danger of non-conformity, which can lead to legal responsibilities and safety and security hazards.
Furthermore, keeping conformity not only safeguards structural honesty yet also improves a business's reputation in the market. Stakeholders and customers are more likely to depend on companies that constantly demonstrate a dedication to top quality and safety and security with rigorous conformity. Thus, making certain compliance standards is a crucial component in the successful execution of welding in commercial applications.
Lowering Maintenance Prices
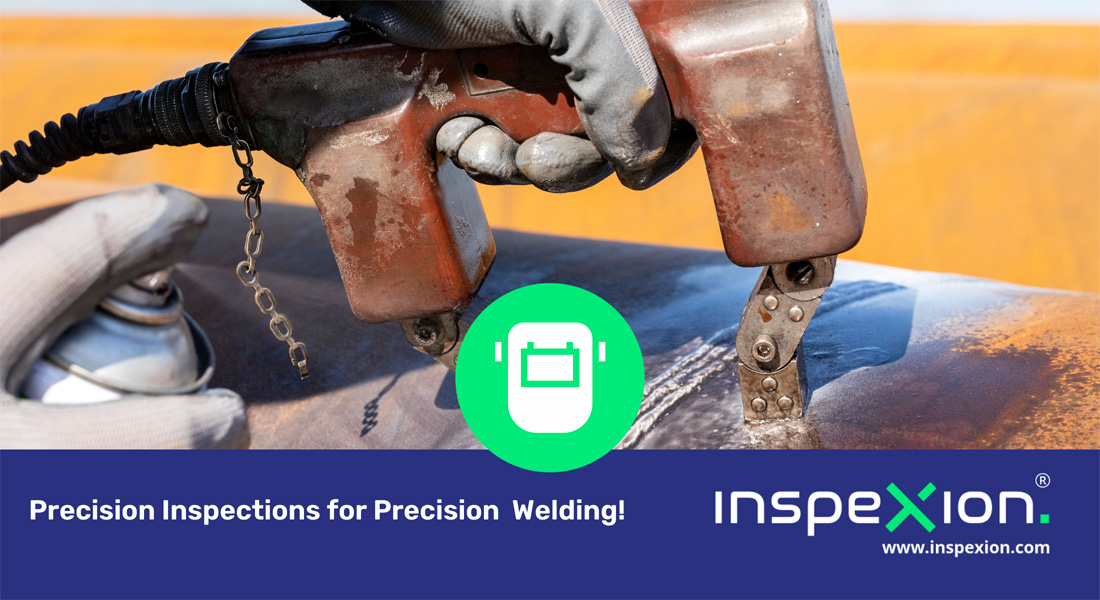
The application of innovative non-destructive testing (NDT) techniques, consisting of ultrasonic, radiographic, and magnetic bit inspections, improves the capacity to find subsurface defects without compromising the structural stability of elements. By using these techniques, sectors can dramatically expand the life span of their equipment, decreasing downtime and the linked financial burden of maintenance tasks.
In addition, a durable welding evaluation routine sustains the optimization of maintenance timetables, shifting from reactive to anticipating upkeep approaches. This aggressive approach not only curtails unanticipated failings but additionally streamlines resource allocation, making sure that upkeep efforts are focused and efficient. Ultimately, the financial investment in extensive welding examination is balanced out by the significant cost savings understood via decreased maintenance demands, contributing positively to the general operational performance of commercial ventures.
Improving Precaution
Welding assessment plays a critical function in this from this source context, as it guarantees that all joints and links satisfy strict safety and security standards. Comprehensive inspections help recognize issues such as splits, porosity, or incomplete combination that could endanger architectural honesty.
Techniques like ultrasonic screening, radiographic screening, and magnetic fragment inspection allow for thorough assessment without damaging the structure. Carrying out a durable top quality control system that consists of normal training for inspectors and welders guarantees adherence to established safety and security criteria.
Finally, promoting a culture of safety within the organization highlights the significance of thorough welding examinations. Motivating open communication and cooperation amongst engineers, inspectors, and welders adds to a shared dedication to security excellence. Welding Inspection Madison. In doing so, markets can guard their procedures, protect personnel, and maintain public trust fund

Final Thought
Detailed welding examination is indispensable in commercial applications, dramatically improving structural honesty and reliability. Ultimately, the diligent implementation of welding inspections plays an important role in keeping functional efficiency and safety and security in industrial settings.
As we check out the diverse advantages of thorough welding examinations, one should take into consideration the broader effects on safety and security, dependability, and cost-effectiveness in industrial procedures.
The primary objective of welding examination is to ensure that the welds are qualified of birthing the expected loads and tensions they will certainly come across in service. Effective welding evaluation plays an important function in reducing these expenses by guaranteeing the integrity and longevity of welds, consequently alleviating the risk of early failures.Comprehensive welding assessment is crucial in commercial applications, dramatically improving architectural stability and integrity. Ultimately, the attentive implementation of welding assessments plays an important duty in keeping operational effectiveness and safety and security in commercial settings.